Digitalizzarsi per rimanere competitive. È questa la chiave su cui le aziende dell’industria manifatturiera dovrebbero puntare oggi e nei prossimi anni. Una tendenza confermata anche dagli obiettivi del Piano Nazionale di Ripresa e Resilienza (PNRR).
Il PNRR è il documento predisposto dal governo italiano per illustrare come il nostro paese intende investire i fondi del programma europeo Next Generation EU e rilanciare l’economia dopo l’emergenza Covid. Obiettivo: incentivare il Made in Italy e la crescita delle piccole, medie e grandi imprese italiane sui mercati esteri.
Alcune delle iniziative promosse nel piano riguardano anche la digitalizzazione delle aziende, da attuare attraverso:
- l’adozione di tecnologie innovative,
- gli investimenti per migliorare le competenze digitali,
- la promozione della transizione digitale.
E in ambito industriale? La via indicata dagli esperti è la fabbrica intelligente o Smart Factory: un’azienda che sfrutta le nuove tecnologie per integrare e coordinare persone e processi produttivi, grazie alla raccolta e all’analisi di dati, e ottenere così ulteriori informazioni preziose, secondo i principi dell’industria 4.0
In questo approfondimento, facciamo il punto sullo stato della digitalizzazione delle aziende manifatturiere italiane: approfondiamo alcune delle principali tecnologie applicate al settore industriale e quali sono i benefici – e gli ostacoli – alla piena realizzazione della Smart Factory.
Smart Factory: i 9 pilastri per la transizione delle aziende verso l’industria 4.0
Col termine industria 4.0 si intende una visione di azienda manifatturiera innovativa, in cui le tecnologie digitali vengono applicate ai processi e alle fasi operative aziendali.
Affinché questo approccio sia possibile, l’impresa deve seguire un percorso di transizione, che il Boston Consulting Group (BGC) – multinazionale statunitense di consulenza strategica – ha sintetizzato in 9 pilastri:
1 – Automazione avanzata dei macchinari e integrazione di dati e sistemi
Nell’azienda manifatturiera 4.0, i reparti e le funzioni fanno parte di un unico sistema integrato.
2 – Impiego della robotica nella catena di produzione
Al fianco degli operatori umani, nella Smart Factory lavorano anche robot autonomi, flessibili e cooperativi che non solo svolgono compiti complessi, ma imparano dalle persone.
3 – Realtà aumentata
L’organizzazione può contare su sistemi basati sulla realtà aumentata, che rendono più rapidi e veloci, per esempio, la selezione di articoli a magazzino, l’invio di istruzioni per eseguire le riparazioni, l’analisi dello stato di salute di un macchinario.
4 – Simulazione
Le simulazioni – applicate sia in fase di ingegnerizzazione che nella produzione – permettono di analizzare in tempo reale i dati raccolti, creare modelli virtuali, e di testare e ottimizzare le prestazioni di macchine, prodotti e processi, identificando eventuali problemi prima che si verifichino.
5 – Produzione additiva
Grazie alla stampa 3D, l’azienda può realizzare più facilmente dei prototipi e produrre piccoli lotti personalizzati.
6 – Internet of Things (IoT)
Nell’azienda che sceglie l’industria 4.0, sensori e dispositivi mettono in comunicazione macchinari e prodotti, ottenendo dati in tempo reale, che possono essere analizzati anche da remoto.
7 – Tecnologie Cloud based
Lo scambio di dati è alla base dell’azienda connessa e grazie al cloud diventa ancora più semplice e veloce, facilitando la comunicazione tra i sistemi informativi aziendali.
8 – Cyber Security
L’apertura al cloud e una maggiore interconnessione devono essere accompagnati da sistemi di protezione più efficienti e sicuri.
9 – Big data e analytics
L’organizzazione raccoglie e analizza dati provenienti da tante fonti diverse (macchinari di produzione, ERP, gestionale clienti…) creando un database di informazioni utile a prendere decisioni più efficaci, in tempo reale.
Applicare i 9 pilastri dell’industria 4.0 significa quindi mettere in atto una vera e propria rivoluzione, non sempre semplice da attuale, soprattutto in Italia, dove il tessuto economico è prevalentemente costituito da PMI.
Qual è dunque la situazione nel nostro paese? Quante imprese manifatturiere italiane hanno scelto la via della Smart Factory e quali iniziative hanno favorito l’adozione del modello 4.0?
Abbiamo raccolto i risultati di diversi studi autorevoli per dipingere un quadro il più possibile aggiornato della situazione in Italia.
Digitalizzazione dell’industria manifatturiera italiana, prima e dopo la pandemia
Secondo l’ultima indagine realizzata da EY sullo stato di digitalizzazione delle aziende manifatturiere italiane – Digital Manufacturing Maturity Index 2019, che risale quindi a prima della pandemia –, in fase pre-Covid, solo una parte minoritaria delle organizzazioni intervistate dalla società di consulenza si era effettivamente mossa verso la transizione 4.0
Infatti, su 150 imprese industriali con un fatturato superiore ai 10 milioni di euro e appartenenti a diversi settori produttivi, solo il 14% dichiarava di aver raggiunto uno stato più avanzato di digitalizzazione. Le iniziative introdotte dalle aziende più virtuose, sotto il profilo dell’innovazione, comprendevano progettualità 4.0 evolute, sistemi informativi in grado di scambiare informazioni con l’ERP (o il cloud) e l’integrazione delle informazioni lungo tutto il processo produttivo. Il restante 86% delle intervistate, invece, si divideva tra organizzazioni che iniziavano a gettare le basi per la digitalizzazione dei processi (49%) e aziende che si trovavano ancora all’inizio del percorso e in fase sperimentale (37%).
E con la pandemia?
Le aziende hanno colto l’opportunità per investire nella digitalizzazione.
“Quasi la metà delle imprese dell’Unione Europea riferisce di aver investito nella digitalizzazione come risposta alla pandemia: è quanto evidenzia il nuovo rapporto della Banca Europea per gli Investimenti (BEI, o EIB in inglese) Digitalisation In Europe 2021-2022: Evidence from the EIB Investment Survey.” (Fonte: Digitalizzazione delle imprese, l’allarme della BEI: con la pandemia è cresciuto il gap tra campioni e aziende al palo, Innovation post).
Intelligenza artificiale (IA o AI), robotica e Internet of Things (IoT) sono tre delle tecnologie più interessate da questo trend positivo.
Dalla manutenzione predittiva al controllo della supply chain: alcune delle applicazioni più interessanti dell’intelligenza artificiale
Secondo l’Osservatorio Artificial Intelligence della School of Management del Politecnico di Milano, nel 2021 gli investimenti nell’Intelligenza artificiale sono cresciuti del 27% per un valore di 380 milioni di euro. Di questi, il 76% ha riguardato investimenti commissionati da aziende italiane e il 24% l’export di progetti, toccando diversi ambiti, dai servizi all’industria.
Uno dei campi in cui l’intelligenza artificiale si è dimostrata più efficace in ambito manifatturiero è la manutenzione predittiva.
Grazie agli algoritmi di analisi dell’immagine (computer vision) – sempre più precisi – oggi è possibile rilevare con maggiore facilità i difetti di produzione; mentre gli algoritmi di analisi dati permettono di prevedere guasti e malfunzionamenti futuri più rapidamente, riducendo le spese di riparazione e manutenzione straordinaria.
Usare un modello di apprendimento automatico basato sui dati storici di produzione, permette all’azienda di pianificare i fermi macchina e di evitare interruzioni improvvise (e molto costose).
A queste applicazioni dell’intelligenza artificiale, si aggiungono anche:
- L’ottimizzazione della supply chain
L’apprendimento automatico riduce la complessità e le risorse impiegate per gestire fornitori e trasportatori: aiuta così a garantire consegne rapide, mantenendo inalterata la qualità del prodotto, con costi di approvvigionamento bassi. - Una migliore capacità di prevedere il rendimento produttivo
L’intelligenza artificiale può essere usata per sapere in anticipo se si verificheranno modifiche al prodotto in uscita dal processo di produzione (per esempio, a causa di un cambiamento delle materie prime utilizzate o di variazioni della temperatura e altri fattori ambientali). - La possibilità di migliorare la prototipazione meccanica
Sia in ambito automotive, che nel mondo della meccanica industriale, l’intelligenza artificiale viene usata per creare automi a cui dare in pasto l’enorme quantità di dati storici raccolti in vari progetti e prevedere la durata dei test. L’obiettivo è ottimizzare la pianificazione delle risorse per più progetti contemporaneamente, migliorando i tempi e i costi di realizzazione dei prototipi e aumentando la produttività delle risorse.
Robotica: investimenti e utilizzi nel settore manifatturiero
Un’altra indagine di settore, condotta nel 2021 da Reichelt Elektronik e OnePoll su un campione di oltre 1.500 aziende del settore manifatturiero – di cui 250 sul territorio italiano – mostra che anche gli investimenti in robotica (in particolare nella robotica collaborativa) hanno avuto un trend positivo.
Il 46% delle aziende manifatturiere intervistate ha affermato che l’uso dei robot è una leva per aumentare la loro competitività. Il 90% delle PMI italiane invece ha dichiarato di lavorare già con i robot, che vengono impiegati in molte operazioni, tra cui lavori di giunzione, taglio, assemblaggio e pallettizzazione, preparazione di materiali, logistica di magazzino e imballaggio. Inoltre, il ricorso ai robot, in molte aziende, è noto dall’esigenza di liberare i lavoratori da compiti fisicamente impegnativi o ripetitivi.
Tuttavia, il 40% degli intervistati ha sollevato delle criticità: sono in molti a ritenere che sia necessario addestrare i dipendenti – attuali e futuri – su come utilizzare la robotica. Mentre il 37% ha rilevato che l’implementazione di nuovi robot procede lentamente a causa della mancanza di competenze tecniche.
Internet Of Things nel settore industriale: +66% di investimenti per la Smart Factory
Secondo l’indagine del 2021 condotta dall’Osservatorio Internet of Things del Politecnico di Milano, anche gli investimenti in questo campo, post-pandemia, sono stati molto positivi. Il mercato globale dell’IoT ha raggiunto un valore di 7,3 miliardi di euro, con un aumento del 20% rispetto al 2020. Di questi 7,3 miliardi, 3 hanno riguardato i servizi, con un aumento del 25% rispetto al 2020. Tra le applicazioni più richieste: servizi informativi, seguiti da energy management e manutenzione preventiva e predittiva.
Inoltre, sono stati investiti 640 milioni nella Smart Factory, con un aumento del 66% rispetto all’anno precedente e applicazioni che vanno dalla manutenzione predittiva, alla diagnosi da remoto e l’assistenza al cliente.
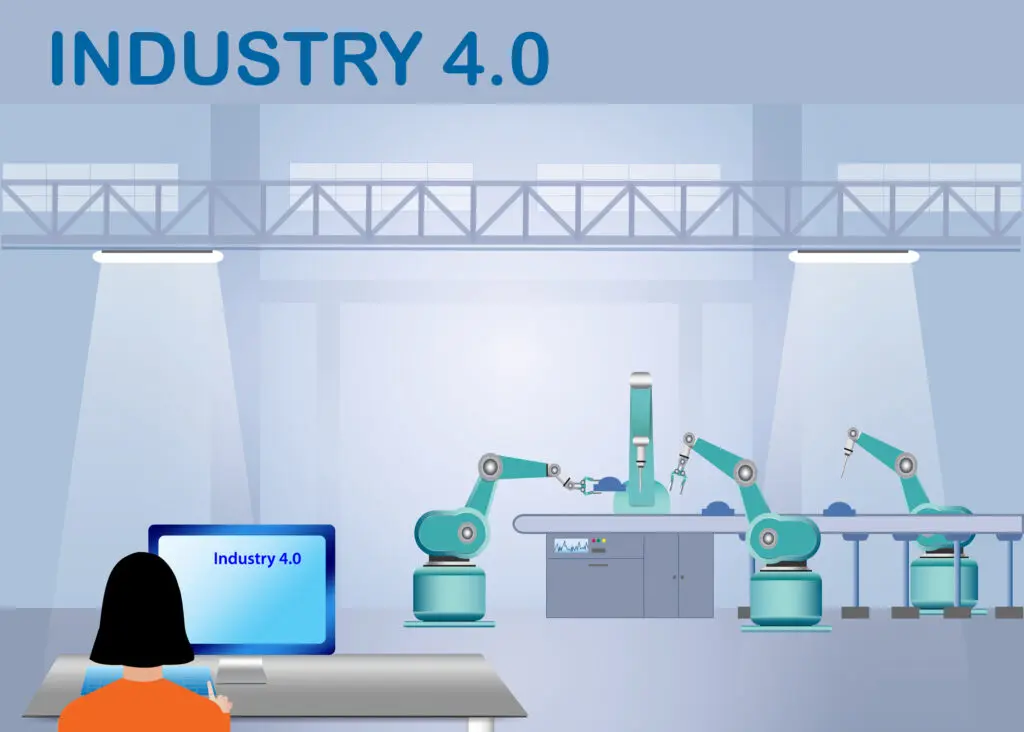
Ottimizzazione, efficienza, velocità: i vantaggi della digitalizzazione nelle aziende manifatturiere
Maggiore efficienza produttiva, previsione di guasti e riduzione dei fermi macchina, riduzione delle spese di manutenzione straordinaria, ottimizzazione della supply chain, prototipizzazione più efficace. Come abbiamo visto sono numerose le attività che traggono grande beneficio dalla transizione verso l’industria 4.0.
A queste si aggiungono anche altri effetti positivi, trasversali a tutte le aziende, e tipici della digitalizzazione. L’adozione di tecnologie digitali infatti rende i processi più veloci, migliora il time-to-market e aiuta le aziende a soddisfare le richieste mutevoli del mercato, garantendo una maggiore competitività e soddisfazione dei clienti, anche in situazioni di crisi.
Lo dimostra quanto accaduto durante la pandemia di Covid-19. In pieno lock-down, infatti, solo le aziende già dotate di un adeguato livello di digitalizzazione e automazione hanno potuto rispondere alle richieste del mercato, pur contando su un numero limitato di collaboratori. (Fonte: “PNRR: il ruolo del digitale nella trasformazione del manifatturiero”, e-guida di Network Digital 360 in collaborazione con Vodafone Business).
Dunque, la transizione digitale non è solo un motore per crescere e competere con successo, è anche una leva indispensabile nell’assicurare la continuità del business.
Eppure, molte aziende italiane non investono ancora nella digitalizzazione e quelle che lo fanno non raggiungono sempre il successo sperato.
Gli ostacoli più comuni alla digitalizzazione dell’industria manifatturiera in Italia
Mancanza di competenze digitali, resistenza al cambiamento, scarsità di investimenti sono spesso i principali freni alla digitalizzazione in azienda.
Carenza di competenze
Come abbiamo già visto, il 40% delle aziende intervistate da Reichelt Elektronik e OnePoll, pensa che sia necessario addestrare i dipendenti sull’uso della robotica e il 37% ritiene che l’implementazione di nuovi robot sia lenta a causa della mancanza di competenze tecniche.
Un dato confermato anche dall’indagine di EY del 2019, secondo cui solo il 12% delle aziende intervistate aveva seguito un programma strutturato per lo sviluppo di skill digitali. E allo stesso tempo, l’84% degli intervistati denunciava una carenza di figure professionali adeguate.
Resistenza al cambiamento e mancanza di comunicazione
Tra gli ostacoli alla digitalizzazione registrati nelle aziende italiane, vi sono poi spesso difficoltà nel coinvolgere tutte le persone interessate. In ambito industriale, infatti, nel momento in cui viene scelta una nuova tecnologia, è importante che i dipartimenti IT e Operations comunichino fra loro.
Il primo è fondamentale per analizzare le possibili sfide nell’implementazione del software, il secondo per stimare il valore aggiunto che la soluzione porterà all’azienda. Tuttavia, questo non sempre avviene, ostacolando di fatto l’adozione di nuove tecnologie.
È importante ricordare che la trasformazione digitale richiede prima di tutto un cambiamento culturale all’interno dell’organizzazione. Non è sufficiente implementare la tecnologia, è necessario rivedere e migliorare i processi aziendali, perché il digitale è un abilitatore di nuovi processi. Se questi sono inefficienti e i reparti aziendali non comunicano, la tecnologia non sarà di aiuto, anzi, il rischio è di incorrere in quella che viene chiamata la digitalizzazione degli sprechi.
Scarsità di investimenti e dimensione aziendale
Il report di EY del 2019 e gli altri studi richiamati in questo approfondimento evidenziano come la dimensione aziendale sia ancora determinante nella capacità di investire nell’industria 4.0. Infatti, se la maggior parte delle grandi aziende ha adottato un piano di sviluppo chiaro verso la digitalizzazione, non si può dire lo stesso per le PMI.
In questo scenario, gli incentivi statali sono stati determinanti nell’adozione di nuove tecnologie.
Il ruolo degli incentivi nella digitalizzazione delle aziende manifatturiere
Nel 2022, TeamSystem ha condotto un’indagine in collaborazione con Kantar per analizzare la situazione dell’Industria 4.0 in Italia, rispetto al Piano di transizione 4.0: il piano avviato con la Legge di Bilancio 2022 che prevedeva una serie di agevolazioni per le imprese che investono in innovazione.
Fra le più importanti ricordiamo la misura Beni strumentali (“Nuova Sabatini”), il credito d’imposta per investimenti in beni strumentali e il credito d’imposta formazione 4.0:
- La Nuova Sabatini è un’agevolazione che punta a sostenere gli investimenti delle aziende, facilitando l’accesso al credito. Permette infatti di acquisire a condizioni favorevoli macchinari, attrezzature, impianti, beni strumentali, hardware, software e tecnologie digitali attraverso l’acquisto o il leasing.
- Il credito d’imposta per investimenti in beni strumentali è una misura che ha l’obiettivo di supportare e incentivare le imprese che investono in beni strumentali nuovi, materiali e immateriali, funzionali alla trasformazione tecnologica e digitale dei processi produttivi.
- Il credito d’imposta formazione 4.0 è un’agevolazione nata per aiutare le aziende nella transizione digitale, incoraggiando l’acquisizione di competenze indispensabili per adottare il modello 4.0.
La nuova Legge di Bilancio 2023, tuttavia, non include le misure necessarie per mantenere le percentuali agevolative previste nel 2022. Al momento sono al vaglio rifinanziamenti per la Nuova Sabatini e il bonus formazione 4.0 che, stando alle stime, dovrebbero essere stanziati a breve.
Digitalizzazione: motore della crescita industriale
L’83% delle aziende intervistate da TeamSystem e Kantar nel 2022, ha beneficiato degli incentivi fiscali, ritenuti fondamentali, per automatizzare o digitalizzare i processi.Questi hanno generato un significativo aumento del fatturato (+56%) per la metà delle imprese, grazie alla maggiore quantità di ordini ricevuti, all’aumento della liquidità e alla riduzione della pressione fiscale: i dati dimostrano quanto la digitalizzazione possa essere una leva importante per la crescita del tessuto industriale italiano, anche nel contesto globale.
In NordEst Informatica, aiutiamo le imprese manifatturiere a implementare innovazioni e tecnologie di ultima generazione.
Stai cercando un sistema che aiuti la tua organizzazione nella transizione verso l’industria 4.0? La soluzione per te potrebbe essere Factory Control di Team System Industry 4.0: un sistema di controllo che raccoglie e gestisce tutte le informazioni necessarie al funzionamento delle officine meccaniche e degli impianti a controllo numerico presenti nello stabilimento. Mette in comunicazione i reparti di produzione con il resto dell’azienda, facilitando lo scambio di informazioni, ottimizzando i costi e accorciando i tempi di setup degli impianti produttivi.
Contattaci senza impegno, saremo felici di conoscere la tua azienda e di individuare insieme a te la soluzione più adatta a raggiungere i tuoi obiettivi.